

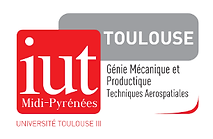
PROPELLER-PRODUCED THRUST
An aircraft propeller or airscrew[1] converts rotary motion from a piston engine, a turboprop or an electric motor, to provide propulsive force. Its pitch may be fixed or variable. Early aircraft propellers were carved by hand from solid or laminated wood, while later propellers were constructed of metal. Modern designs use high-technology composite materials.
The propeller attaches to the crankshaft of a piston engine, either directly or through a reduction unit. A light aircraft engine may not require the complexity of gearing, which is essential on a larger engine or on a turboprop aircraft.
Italian scientist Leonardo da Vinci made sketches of an “air screw” human-powered helicopter with no practical application between 1487 and 1490.
The twisted airfoil (aerofoil) shape of an aircraft propeller was pioneered by the Wright Brothers. While some earlier engineers had attempted to model air propellers on marine propellers, the Wright Brothers realized that a propeller is essentially the same as a wing, and were able to use data from their earlier wind tunnel experiments on wings, introducing a twist along the length of the blades. This was necessary to maintain a more uniform angle of attack of the blade along its length. Their original propeller blades had an efficiency of about 82%, compared to the 90% of modern propellers. Mahogany was the wood preferred for propellers through World War I, but wartime shortages encouraged use of walnut, oak, cherry and ash.
Alberto Santos Dumont was another early pioneer, having designed propellers before the Wright Brothers (albeit not as efficient) for his airships. He applied the knowledge he gained from experiences with airships to make a propeller with a steel shaft and aluminium blades for his 14 bis biplane. Some of his designs used a bent aluminium sheet for blades, thus creating an airfoil shape. They were heavily undercambered, and this plus the absence of lengthwise twist made them less efficient than the Wright propellers. Even so, this was perhaps the first use of aluminium in the construction of an airscrew.
Originally, a rotating airfoil behind the aircraft, which pushes it, was called a propeller, while one which pulled from the front was a tractor. Later the term 'pusher' became adopted for the rearmounted device in contrast to the tractor configuration and both became referred toas 'propellers' or 'airscrews'.
The understanding of low speed propeller aerodynamics was fairly complete by the 1920s, but later requirements to handle more power in a smaller diameter have made the problem more complex.
Since the 1940s, propellers and propfans with swept tips or curved "scimitar-shaped" blades have been studied for use in high-speed applications so as to delay the onset of shockwaves, in similar manner to wing sweepback, where the blade tips approach the speed of sound. The Airbus A400M turboprop transport aircraft is expected to provide the first production example: note that it is not a propfan because the propellers are not mounted directly to the engine shaft but are driven through reduction gearing.
